Custom carpets play an essential role in creating bespoke interiors for both residential and commercial spaces. Unlike mass-produced carpets, custom designs are tailored to fit the specific aesthetic and functional needs of a space, offering a unique level of personalization and craftsmanship. The process of manufacturing a custom carpet is a blend of traditional artistry and modern technology, ensuring that each piece is of high quality and perfectly matches the client’s vision.
This blog will take you through the intricate process of custom carpet manufacturing—from initial design consultations to the final delivery of a beautifully crafted carpet. Whether you’re considering a custom carpet for your home, hotel, or business, understanding each step of the journey will help you appreciate the craftsmanship and effort involved.
Understanding the Custom Carpet Manufacturing Process Journey
The custom carpet manufacturing process involves multiple stages that combine creativity, precision, and technical expertise. Each step is crucial in ensuring that the final product meets the client’s expectations in terms of design, durability, and functionality. The key stages of the manufacturing journey are:
- Client Consultation and Initial Concept Development: Understanding the client’s needs and preferences.
- Design and Customization Process: Creating a unique design based on the client’s vision.
- Material Selection: Choosing the right materials for durability and aesthetics.
- Yarn Spinning and Dyeing: Preparing the yarn with specific colors and textures.
- Weaving and Tufting Process: Bringing the design to life through various weaving techniques.
- Backing and Finishing: Adding durability and final touches.
- Quality Control and Testing: Ensuring the carpet meets industry standards and client expectations.
- Packaging and Delivery: Preparing and shipping the final product to the customer.
Each of these stages involves careful planning and coordination between designers, craftsmen, and manufacturers, ensuring the final product is not just a piece of décor but a statement of luxury and quality.
Stage 1: Client Consultation and Initial Concept Development
The first step in custom carpet manufacturing begins with an in-depth consultation between the client and the design team. This is a crucial phase where the design team gathers information on the client’s preferences, space requirements, and overall vision for the carpet.
Factors such as the size of the space, the purpose of the carpet (whether for aesthetic or functional use), and the desired color schemes and patterns are discussed.
Clients often come with a general idea of what they want, but the design team helps refine and translate this vision into something tangible.
Through mood boards, color palettes, and material samples, the designers collaborate with the client to develop a cohesive concept that fits the space’s aesthetic. This phase may also involve site visits to better understand how the carpet will interact with the interior design and existing décor.
Collaboration and Customization
Collaboration is key during this stage. Designers work closely with clients to ensure that their unique needs are met, whether it’s for a grand hotel lobby, an executive office, or a private residence.
Every aspect, from the choice of materials to the pattern details, is discussed in this phase to ensure the client’s ideas are brought to life. The level of customization in this stage sets the foundation for the entire manufacturing process, making it a highly personalized experience.
A company like Shivalika Rugs, for instance, excels in this collaborative process, utilizing its fully integrated production facility. Spanning 200,000 square feet in Panipat, Allowing it for complete control over every aspect of production—from design to delivery.This seamless integration enables a smooth, eco-friendly approach throughout the manufacturing journey, ensuring the client’s vision is not only met but exceeded.
Stage 2: Design and Customization Process
Once the client’s needs and preferences are clear, the design team begins creating the actual patterns, motifs, and textures that will be incorporated into the custom carpet. Digital design software is often used to visualize the designs, allowing the client to review and approve before the manufacturing process begins.
The level of customization can vary greatly. Some clients prefer minimalistic designs, while others may request intricate patterns inspired by traditional or cultural themes. The design team must be creative yet practical, ensuring that the chosen design will translate well into a durable, functional carpet.
Incorporating Brand Identity in Custom Carpets
Incorporating a client’s brand identity is a common practice in custom carpet manufacturing, especially for commercial and corporate spaces. Hotels, retail stores, and offices often use custom carpets as a way to reflect their brand values and aesthetics. A well-designed carpet can subtly reinforce a company’s branding through colors, patterns, and textures that align with the overall corporate identity.
Stage 3: Material Selection
The choice of materials is one of the most important aspects of custom carpet manufacturing. Different fibers offer varying levels of durability, comfort, and visual appeal. The most common materials used in custom carpets are wool, nylon, silk, and other synthetic blends. Each material has its strengths, and the selection process involves balancing factors like budget, durability, softness, and sustainability.
- Wool: Known for its durability and natural feel.
- Nylon: Durable and stain-resistant, great for high-traffic areas.
- Silk: Luxurious and soft, typically used in high-end designs.
Sustainable and Eco-Friendly Options in Carpet Manufacturing
As sustainability becomes increasingly important in design, many custom carpet manufacturers now offer eco-friendly options. Natural fibers like wool and jute are sustainable choices, and recycled synthetic fibers are also becoming popular.Shivalika Rugs, prioritize environmentally harmonious production methods, incorporating sustainable practices into their operations. It ensures that every rug not only adheres to the highest standards of quality but is also crafted with the environment in mind.
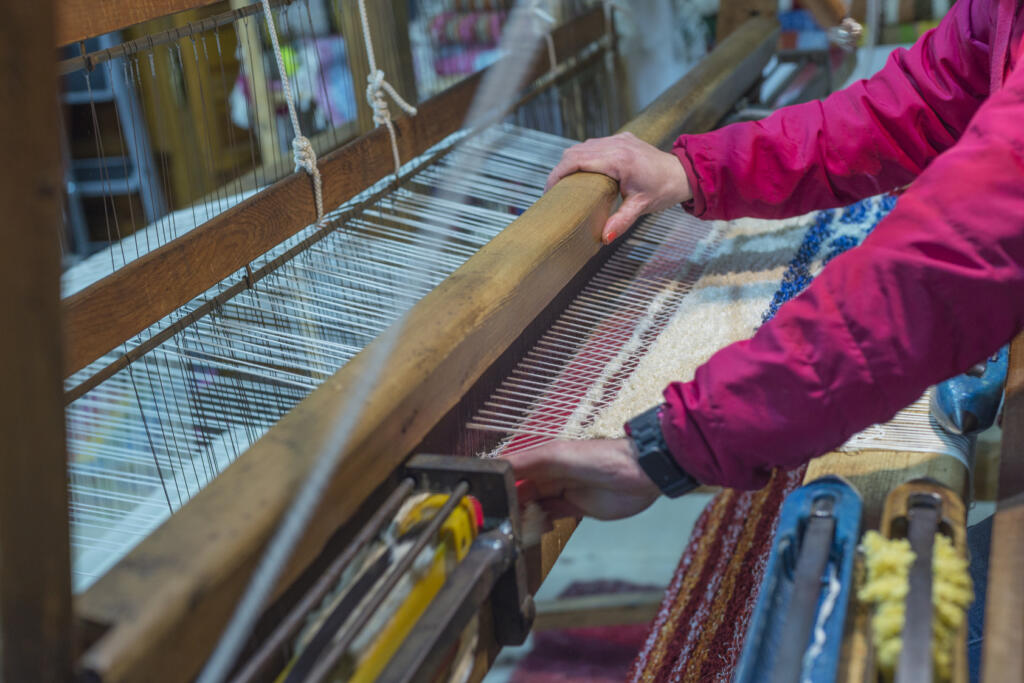
Stage 4: Yarn Spinning and Dyeing
Once the design and materials are chosen, the next step involves preparing the yarn. Yarn spinning is a process where fibers are twisted together to form a continuous thread. This thread will later be used in the weaving or tufting process. The texture and thickness of the yarn can vary based on the client’s preferences for how the carpet should feel underfoot.
Dyeing the yarn is another critical process, as color consistency and vibrancy are key to creating a visually appealing carpet. The yarn can be dyed using a variety of methods, depending on the material and the desired outcome.
Modern Dyeing Techniques and Innovations
With advancements in technology, modern dyeing methods now allow for greater precision in achieving the exact shade and color variation the client desires. Digital dyeing, for example, provides superior control and ensures that each batch of yarn is identical in color.
Stage 5: Weaving and Tufting Process
The weaving or tufting stage is where the carpet begins to take its final form. Weaving involves interlacing yarns to create a tight, structured fabric, while tufting involves pushing yarn through a backing material to form loops or cuts, which are then secured in place.
There are different methods of weaving, with hand-tufting and machine-tufting being the most common. Hand-tufting is a more labor-intensive process and often used for high-end, bespoke carpets, while machine-tufting allows for faster production and is commonly used in commercial applications.
Stage 6: Backing and Finishing
Once the weaving or tufting process is complete, the carpet needs to be backed and finished. The backing adds stability and ensures that the carpet maintains its shape and durability over time. There are different types of backing materials available, from felt to latex, each with its own benefits.
Stage 7: Quality Control and Testing
Quality control is an integral part of custom carpet manufacturing. Throughout the process, the carpet undergoes rigorous testing to ensure it meets both the client’s expectations and industry standards. These tests include checking for color consistency, texture quality, and overall durability.
Stage 8: Packaging and Delivery
After passing quality control, the custom carpet is carefully packaged and prepared for delivery. Shivalika Rugs, known for their efficient in-house logistics, ensures that their carpets reach their destination in perfect condition, reflecting the company’s commitment to quality and customer satisfaction.
The Future of Custom Carpet Manufacturing
The future of custom carpet manufacturing is bright, with advancements in technology continually improving the efficiency and quality of production. 3D printing technology is starting to influence the industry, allowing for even more detailed and intricate designs. Additionally, the demand for sustainable carpets is driving innovation in eco-friendly materials and production methods.
Conclusion
The journey from design to delivery in custom carpet manufacturing is a detailed, collaborative process that ensures every piece is unique and perfectly suited to the client’s needs. By combining traditional craftsmanship with modern technology, companies like Shivalika Rugs are setting new benchmarks in quality, sustainability, and innovation. Custom carpets, whether for a luxury residence, a boutique hotel, or a corporate office, elevate the aesthetic and feel of any space. Investing in a custom carpet is a long-term decision that ensures durability, elegance, and personalization.